塑胶通过注塑成型成为形状多变造型丰富的注塑件产品,广泛应用在汽车、玩具等行业当中,注塑加工过程如果操作不当会导致注塑件出现各种缺陷,注塑件常见缺陷有外观不良、尺寸位置偏差等,细分更有不同的缺陷特点,下面来看看注塑件的常见缺陷和相对应的改善措施。
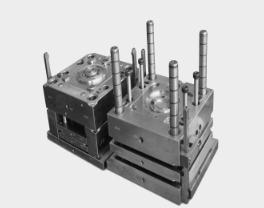
1、成品缩水
注塑件成品缩水常发生在产品壁较厚的地方,因为熔料不同部位在冷却和固化时发生不同程度的收缩导致,如产品侧壁边缘、肋的背面等部位,发生这种情况需要把熔料厚度减低,加大模具的浇口和排气,即将成型时升高料温延长保压时间,避免注塑件缩水现象。
2、表面不洁或出现花纹
注塑时模腔的顶针设计过高会导致成品表面出现亮印,模温过高也容易出现残胶、油渍使得成品表面不洁,注塑射压偏高会导致成品表面出现气纹、拉白、夹水纹等,因此注塑前要对模具内进行杂质清理和打光处理,协调注塑射压和速度,避免注塑件表面有花纹或者粗糙。

3、超出尺寸公差
注塑件如果超过尺寸公差,大概率是模具本身有问题或者成型条件不当造成,应该及时修正模具,如果收缩率不合适导致尺寸偏差过大,需要重开模具改善加胶减胶情况,对成型尺寸影响较大的注压通常是保压和射压的二次压力,因此协调保压和射压的补缩作用可明显改善尺寸不当的现象。
如今注塑加工已经是一种成熟的模具加工工艺,注塑件加工成型的周期也很短,因此越来越多的行业选择注塑模具,厂家生产注塑件时一定要注意产品常见的缺陷和其改善措施,在生产过程中正确操作,尽可能避免缺陷重复性出现,如此可提高厂家生产效率,获得注塑模具客户的更多好评。