对于模具行业必须要不断提高它的制造工艺,与此同时同步提升设计技术,而从整个大的统和发展模式上来说,必须要改变模具加工的样式和发展路线,注重成本的同时尽量的缩短本品的工期,这样更有利于企业进一步的开拓市场,在赢得订单的同时提升口碑也提升技术,促进整个行业的高标准化,这样还可以降低工作人员的重复性劳动率,既提高了企业效率,又让企业确确实实得到实惠,如何对注塑模具加工进行优化?
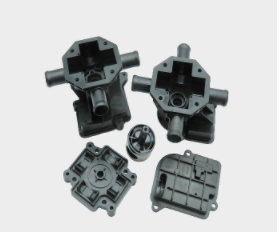
1、工作尺寸计算
问题首先运用成组技术基本原理,对注塑模具结构进行分析,提出模具零件按其功用可分为型腔型芯、模板、结构件和标准件等类零件的分类方法。利用实例,对各类模具零件的结构特点加以阐述,并对结构特点的标识方法进行论述,在此基础上开发一套适用于注塑模具零件的分类编码系统。其次,针对注塑模具成型零件工作尺寸的计算问题开展研究,提出成型零件工作尺寸计算方法比较的准则;运用计算与分析手段,对目前众多的注塑模具成型零件工作尺寸的计算方法进行比较,在塑件尺寸精度满足要求的前提下,中差法是一种既筒捷又准确的成型零件计算方法。
2、组织体系结构优化
根据建立的分类和编码系统的注塑模具加工模具,在分类的基础上,注塑模具零件的结构特点进行了分析,并参数化项目对应的参数提取原理提出相应的代码点的编码;在此基础上,构建了三维参数化地图库。根据模具制造工艺的设计特点和CAPP系统的工作原理,确定了注塑模具CAPP系统的体系结构和注塑模具CAPP系统的功能模块组成,采用模块化设计思想对体系结构进行组织,利用模具零件分类编码系统解决CAPP系统中零件信息的描述和输入问题,研究了数据模型和数据库构建方法,探索了工艺数据库的管理技术,研究了开放式数据库结构的设计模式。
注塑模具加工技术的结构化进程越来越快速,对于模具加工的系统性功能要求越来越高,随着它的整体工艺数据库的拓展,这种数据库又变成了一种行业发展的知识库和工艺文件的库存,带动整体行业的共同进步,而且现在形成了一种新的发展模式,企业和行业的共同进步成为了共识。