注塑过程中的技术和材料选择对于产品的质量至关重要。然而,即使是很先进的注塑技术也无法完全避免缺陷的产生。理解这些常见缺陷及其成因有助于采取预防措施。究竟注塑件在生产过程中常见的缺陷有哪些呢?
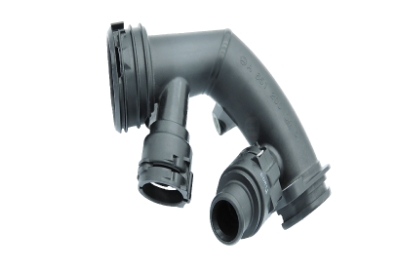
首先,短射是比较常见的问题之一。这种情况发生时,塑料熔料没有充满模具的所有腔体,导致成型不完整。短射通常由料温过低、注射速度或压力不足引起,也可能是由于注塑机的计量不准确或材料流动性不足造成的。
其次,翘曲或变形也是注塑件常见的缺陷。这种缺陷常见于形状复杂或壁厚不均的制品。翘曲的成因通常与模具冷却速度不均、注塑压力过高或材料收缩率不均匀有关。
第三,气泡形成,这是注塑过程中的一个常见问题。气泡的出现通常是由于材料中含有湿气或注射速度太快,使得空气被困在熔体中无法逸出。
接下来,焊接痕是另一个常见缺陷。当两股熔融塑料在模具中汇合时,如果没有充分融合,就会形成焊接痕。这种缺陷通常由注射速度太慢或熔料温度过低引起。
此外,应力裂纹也需要关注。应力裂纹通常发生在注塑件的应力集中区,可能是由于模具设计不当、材料选择错误或脱模过程中的应力过大造成的。
从实际操作中出发,注塑厂家需不断监控和优化制造过程,以降低这些常见缺陷的发生,确保产品质量。正确的材料选择、模具设计及工艺设置是关键。