随着汽车工业的迅速发展,注塑技术已成为制造汽车部件不可或缺的一部分。使用合适的材料不仅可以提升产品的性能,还能确保成本效率。那么,在汽车注塑件制作中,通常会使用哪些材料呢?
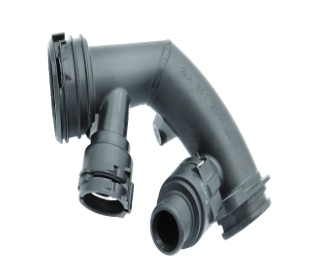
首先,ABS(丙烯腈-丁二烯-苯乙烯共聚物) 是很常用的汽车注塑材料之一。它以其优良的机械性能、良好的冲击强度和易加工性而被广泛应用于汽车内饰件如仪表板、门内饰板等部件。ABS也表现出良好的热稳定性和化学稳定性,使其适合于复杂的汽车部件制造。
其次,聚丙烯(PP),由于其较低的成本和较高的化学稳定性,PP是制作非承重结构汽车部件的优选材料,如保险杠、风扇罩等。PP的另一个优点是它的重量轻,有助于提高燃油效率。
接着,聚碳酸酯(PC),因其卓 越的抗冲击性和透明性,常用于制造汽车灯罩和窗户。PC不仅强度高,而且具有良好的耐热性和耐候性,非常适合需要高度耐用性的应用。
此外,聚酰胺(尼龙,PA) 是另一种常用于汽车部件的材料。尼龙具有高机械强度、耐磨性和耐化学性,常用于制作发动机罩、空气滤清器罩及各种承重部件。
同时,热塑性弹性体(TPE) 也在汽车制造中扮演着重要角色。TPE结合了橡胶的弹性和塑料的加工性能,常用于制作密封件、减震器和软管。
实际应用中,选择正确的材料对于确保汽车注塑件的性能和耐久性至关重要。材料的选择应基于部件的具体用途和性能要求。正确的材料能有效提升产品质量和成本效益。